Toolpaths play a fundamental role in CNC (Computer Numerical Control) machining, enabling precise and efficient cutting operations. A toolpath is a defined route that a cutting tool follows to shape a workpiece. It determines the tool's movement, direction, and engagement with the material. This article provides an in-depth introduction to toolpaths in CNC machines, exploring their types, optimization techniques, and the significance they hold in the world of manufacturing.
What Exactly are Toolpaths?
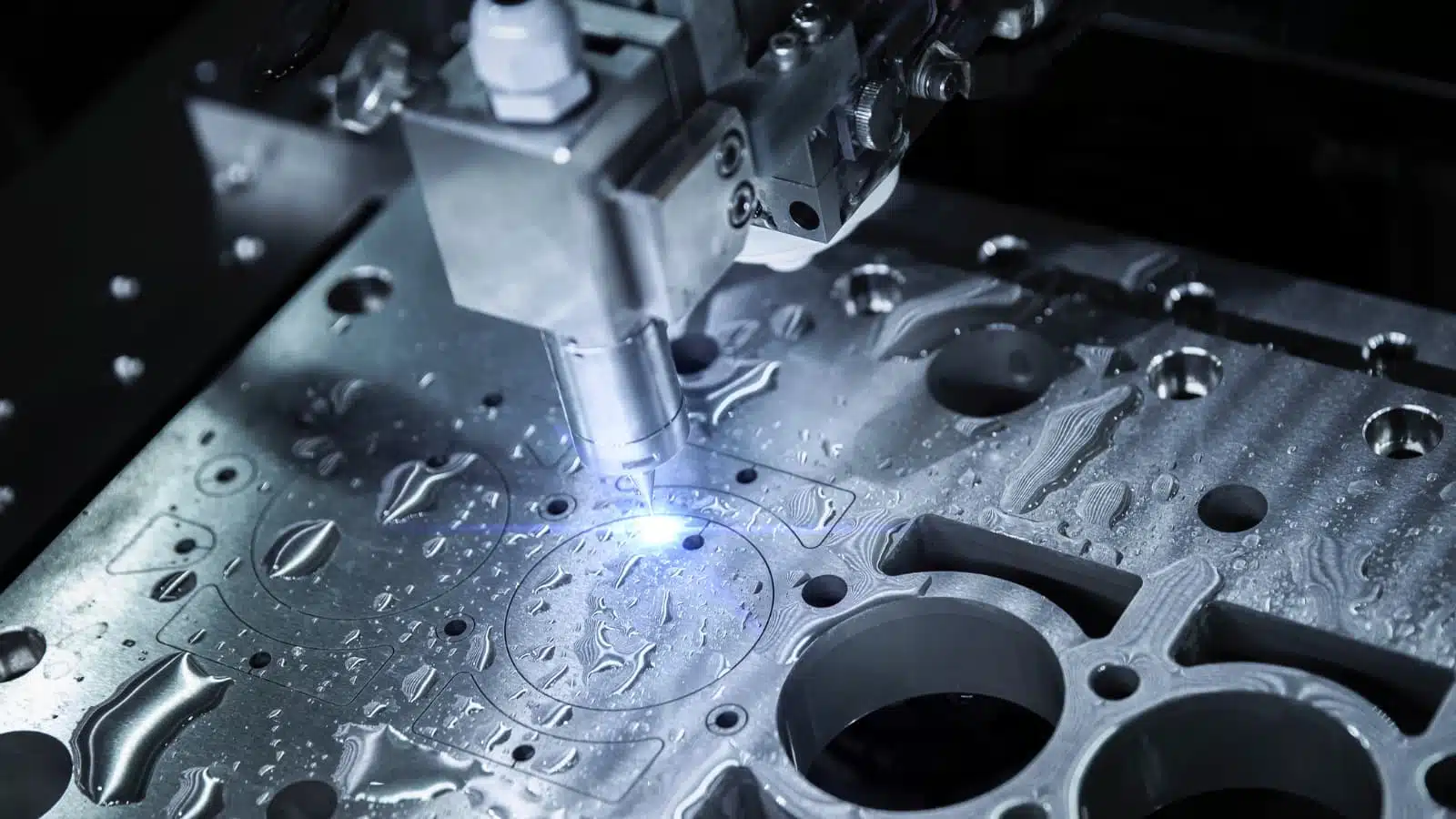
A toolpath is essentially a roadmap for CNC machinery, dictating the path and direction a cutting tool follows to transform a digital design into a physical part. It is a series of coordinate locations through which the tool moves in the machining process, influenced by the geometry of the part to be machined, the capabilities of the machine itself, and the desired outcome of the machining process.
Importance of Toolpaths in CNC Machining
Toolpaths are crucial in CNC machining as they directly impact the quality, accuracy, and efficiency of the final product. Proper toolpath selection and optimization can significantly reduce machining time, minimize material waste, and improve the surface finish of the workpiece. Lunyee's processing equipment has been optimized over the years, and it can provide high-precision, high-quality processing results, especially the vertical machining center.
Fundamental Types of Toolpaths
- 2D Toolpaths: In 2D toolpaths, movements are confined to the x and y axes, usually for operations on flat surfaces.
- 2.5D Toolpaths: These add depth to 2D toolpaths by incorporating multiple z-axis depths, allowing for the machining of simple prismatic parts with varying levels.
- 3D Toolpaths: Here, tool movements extend to all three axes (x, y, and z), enabling the creation of parts with complex geometries and curved surfaces.
- 4-Axis and 5-Axis Toolpaths: Incorporating rotational axes (A, B, or C) in addition to the linear x, y, and z axes, these toolpaths allow for even more complex part geometries to be machined, often enabling access to features that are not possible with 3-axis machining alone.
- 3+2 Toolpaths: These toolpaths utilize rotational axes to position a part for subsequent machining with 3-axis toolpaths, allowing for efficient multi-face machining without full simultaneous 5-axis movements.
Dynamic Toolpaths to Optimize CNC Machining
Understanding and selecting the right toolpath is crucial for enhancing machining efficiency and productivity. CAD/CAM technologies greatly facilitate this by offering a variety of dynamic toolpaths tailored to specific machining needs, such as:
- Face: Achieves excellent finishing on the face of a part.
- Constant Stepover: Provides a consistently smooth finish across a surface.
- Pencil Milling: Addresses corners and concave areas to optimize surface finish.
- Contour: Ideal for machining loops, open pockets, and stick fonts.
- Horizontal Machining: A finishing strategy effective on both flat and sloped areas.
- Rest Machining: Utilizes different cutter sizes for effective roughing and finishing.
- Spiral: Efficiently machines rounded details.
- Advanced Z Level Finishing: 3D finishing toolpath for machining vertical surfaces.
Optimization Techniques for Toolpaths
- High-Speed Machining: High-speed machining optimizes toolpaths to increase the cutting speed without compromising accuracy. This technique reduces machining time, improves surface finish, and extends tool life.
- Adaptive Toolpaths: Adaptive toolpaths dynamically adjust the cutting conditions based on the material, tool, and machine capabilities. By varying the feed rate and depth of cut, adaptive toolpaths optimize the machining process for improved efficiency and reduced tool wear.
- Trochoidal Milling: Trochoidal milling involves using a series of circular tool paths to remove material efficiently. By overlapping the circular paths, trochoidal milling reduces tool stress and increases material removal rates.
- Rest Machining: Rest machining optimizes toolpaths by removing only the material left after previous operations. This technique reduces machining time and minimizes tool wear, as the tool only engages with the remaining material.
Significance in Manufacturing
Toolpaths are critical in achieving the desired precision, efficiency, and quality in CNC machining. By selecting the appropriate toolpath strategies and optimizing them based on the specific requirements of the workpiece, you can enhance their productivity, reduce costs, and achieve higher quality finished products. Toolpath optimization techniques also contribute to extending tool life, minimizing downtime for tool changes, and improving overall process stability.
Conclusion
Toolpaths are crucial in CNC machining, guiding cutting tools' movements and actions to shape workpieces accurately and efficiently. Knowing various toolpath types and optimization methods is vital for maximizing productivity, reducing material waste, and attaining top-notch results.