Multi-axis machining is a manufacturing process that involves the tool moving in four or more directions, typically used for processing parts made of metal or other materials. Unlike traditional three-axis machining, multi-axis machining incorporates additional axes of movement, allowing for more intricate and detailed work on a single machine setup. This article delves into the principles, benefits, challenges, and applications of multi-axis machining, providing a comprehensive understanding of this advanced manufacturing process.
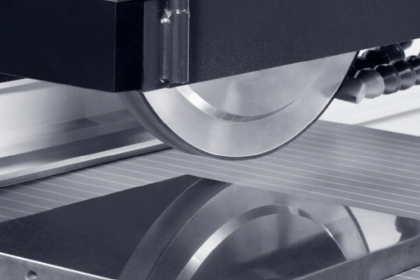
Introduction to Multi-Axis Machining
Multi-axis machining involves the use of computer numerical control (CNC) machines that can move tools and workpieces along multiple axes simultaneously. While traditional CNC machines operate along three axes (X, Y, and Z), multi-axis machines can incorporate up to five or more axes, adding rotational and tilting capabilities. This allows for the machining of complex geometries and intricate features that would be impossible or highly inefficient with conventional methods.
Types of Multi-Axis Machining
- 4-Axis Machining: In addition to the three linear axes (X, Y, Z), 4-axis machines include a rotational axis (A-axis) around the X-axis. This configuration is suitable for operations like drilling and milling on the sides of the workpiece.
- 5-Axis Machining: The most common and versatile form of multi-axis machining, 5-axis machines add two rotational axes (A and B) to the three linear axes. This allows the tool to approach the workpiece from virtually any angle, enabling the machining of highly complex shapes and surfaces.
- 6-Axis and Beyond: Advanced multi-axis machines can include six or more axes, offering even greater flexibility and precision. These machines are often used in highly specialized industries such as aerospace and medical device manufacturing.
Principles of Multi-Axis Machining
Kinematics and Motion Control
The core principle of multi-axis machining is the ability to control multiple axes of movement simultaneously. This requires sophisticated kinematic algorithms and motion control systems to ensure precise coordination between the tool and the workpiece. CNC controllers play a crucial role in managing these movements, converting digital instructions from computer-aided design (CAD) and computer-aided manufacturing (CAM) software into precise tool paths.
Tool Orientation and Positioning
In multi-axis machining, the orientation and positioning of the tool relative to the workpiece are critical. The additional axes provide more degrees of freedom, allowing the tool to maintain optimal contact angles and cutting conditions. This enhances surface finish quality, reduces tool wear, and enables the machining of undercuts, deep cavities, and other challenging features.
Collision Avoidance and Path Planning
With the increased complexity of multi-axis machining comes the risk of collisions between the tool, workpiece, and machine components. Advanced CAM software includes collision detection and avoidance algorithms, ensuring safe and efficient tool paths. Path planning also involves optimizing the sequence of operations to minimize tool changes, reduce machining time, and enhance overall productivity.
Benefits of Multi-Axis Machining
- Increased Precision and Accuracy: Multi-axis machining offers unparalleled precision and accuracy, enabling the production of complex parts with tight tolerances. The ability to approach the workpiece from multiple angles reduces the need for multiple setups and repositioning, minimizing cumulative errors and enhancing dimensional accuracy.
- Enhanced Surface Finish: The continuous engagement of the tool with the workpiece in multi-axis machining results in superior surface finish quality. This is particularly important for applications requiring high aesthetic standards or functional surface properties, such as aerospace components and medical implants.
- Greater Design Flexibility: Multi-axis machining provides greater design flexibility, allowing manufacturers to create intricate geometries, internal features, and organic shapes that would be challenging or impossible with traditional methods. This opens up new possibilities for innovation and product differentiation.
- Reduced Setup and Machining Time: By combining multiple operations into a single setup, multi-axis machining significantly reduces setup time and eliminates the need for repositioning the workpiece. This leads to shorter machining cycles, higher throughput, and improved overall efficiency.
- Cost Savings: While the initial investment in multi-axis machinery and software can be substantial, the long-term cost savings are significant. The reduction in setup time, increased tool life, and enhanced productivity translate into lower per-unit production costs and faster return on investment.
Challenges of Multi-Axis Machining
- High Initial Investment: The cost of acquiring multi-axis CNC machines, along with the necessary software and training, can be a major barrier for small and medium-sized enterprises. However, the long-term benefits and potential for increased productivity often justify the investment.
- Complexity of Programming: Programming for multi-axis machining is more complex than traditional three-axis operations. It requires advanced CAM software and skilled operators who understand the intricacies of toolpath generation, collision avoidance, and machine kinematics. Continuous training and education are essential to maintain proficiency and keep up with technological advancements.
- Tooling and Workholding: Multi-axis machining demands specialized tooling and workholding solutions to ensure stability and precision. The selection of appropriate cutting tools, toolholders, and fixtures is critical to achieving optimal results. Additionally, the increased degrees of freedom necessitate careful consideration of tool reach and clearance to avoid collisions.
- Maintenance and Calibration: The complexity of multi-axis machines requires regular maintenance and calibration to ensure optimal performance. This includes checking and adjusting the alignment of axes, verifying the accuracy of rotary encoders, and maintaining the precision of linear guides and bearings. A proactive maintenance strategy is essential to minimize downtime and extend the lifespan of the equipment.
Applications of Multi-Axis Machining
- Aerospace Industry: The aerospace industry is one of the primary beneficiaries of multi-axis machining. The production of aircraft components, such as turbine blades, engine parts, and structural elements, requires high precision, complex geometries, and superior surface finish. Multi-axis machining meets these demands, enabling the efficient manufacture of lightweight, high-performance components.
- Automotive Industry: In the automotive industry, multi-axis machining is used for the production of engine components, transmission parts, and complex chassis structures. The ability to machine intricate features and maintain tight tolerances enhances the performance and reliability of automotive systems.
- Medical Device Manufacturing: Medical device manufacturing requires the production of components with high precision and complex shapes, such as orthopedic implants, surgical instruments, and dental prosthetics. Multi-axis machining enables the creation of these intricate parts with excellent surface finish and biocompatibility.
- Mold and Die Making: The mold and die industry benefits from multi-axis machining through the efficient production of molds, dies, and tooling with complex geometries and fine details. This enhances the quality of molded products and reduces lead times in manufacturing.
- Energy Sector: In the energy sector, multi-axis machining is used for the production of components for wind turbines, gas turbines, and other power generation equipment. The ability to machine large, complex parts with high precision is essential for ensuring the efficiency and reliability of energy systems.
Future Trends in Multi-Axis Machining
- Integration with Additive Manufacturing: The integration of multi-axis machining with additive manufacturing (AM) techniques is a growing trend. Hybrid manufacturing systems combine the benefits of both subtractive and additive processes, enabling the creation of complex parts with internal features, reduced material waste, and improved performance.
- Automation and Smart Manufacturing: Advancements in automation and smart manufacturing are transforming multi-axis machining. The use of robotic arms for automated workpiece handling, real-time monitoring of machining parameters, and predictive maintenance through IoT technologies are enhancing productivity, quality, and reliability.
- Artificial Intelligence and Machine Learning: Artificial intelligence (AI) and machine learning (ML) are being integrated into CAM software and CNC controllers to optimize tool paths, predict tool wear, and improve process stability. These technologies enable adaptive machining, where the machine can adjust parameters in real-time to achieve optimal performance.
- Sustainable Manufacturing: Sustainable manufacturing practices are gaining importance in the industry. Multi-axis machining contributes to sustainability by reducing material waste, minimizing energy consumption, and enabling the production of lightweight, high-performance components that improve the efficiency of end products.
Conclusion
Compared to two-axis and three-axis machining, the addition of extra motion axes in multi-axis machining allows the equipment to create complex geometric designs and parts that were previously impossible. While the upfront investment cost of multi-axis machining is higher, from a long-term perspective, multi-axis machining has tremendous long-term advantages.