Horizontal machining centers (HMCs) and vertical machining centers (VMCs) are two widely used and highly versatile machine tools. Both HMCs and VMCs play crucial roles in modern manufacturing, offering unique advantages and capabilities. Understanding the differences between these two types of machining centers is essential for selecting the most suitable machine for specific applications. In this article, we will delve into the disparities between horizontal and vertical machining centers, exploring their functionalities, features, and applications, to help you make informed decisions when choosing the appropriate machining center for their manufacturing needs.
Introduction to Machining Centers
Machining centers are advanced CNC machines capable of handling a variety of operations, including milling, drilling, and tapping, all in one setup. They are distinguished mainly by the orientation of the spindle, the component that holds and drives the cutting tools. The orientation of the spindle defines whether the machining center is horizontal or vertical, significantly impacting its operational capabilities and suitable applications.
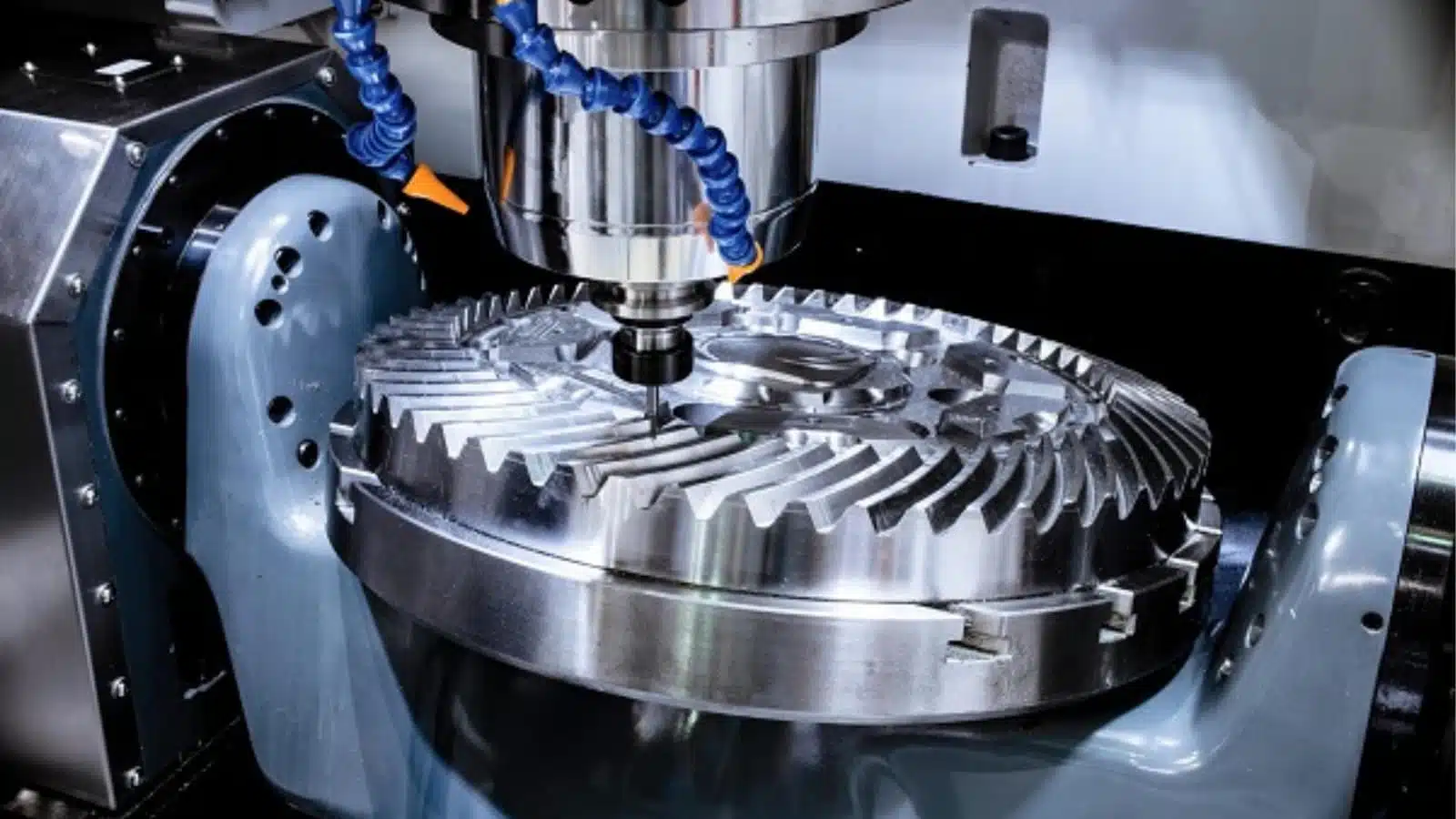
The Essence of CNC Technology
Central to both HMCs and VMCs is CNC (Computer Numerical Control) technology, which allows for the automated control of the machines' movements. This technology enables the machining centers to produce parts with high precision and repeatability, critical in today's manufacturing landscape where efficiency and accuracy are paramount.
Horizontal Machining Centers (HMCs)
Horizontal machining centers feature a spindle oriented horizontally, parallel to the machine's bed. This orientation facilitates the mounting of workpieces on a horizontally aligned table that moves along the X, Y, and sometimes Z axis.
Advantages of HMCs
- Enhanced Chip Evacuation: The horizontal orientation allows gravity to help remove chips from the workpiece, minimizing contamination and tool wear.
- Increased Rigidity and Cutting Force: HMCs generally offer superior rigidity, allowing for heavier cutting forces and therefore faster material removal rates.
- Pallet Changer System: Many HMCs are equipped with a pallet changer that allows for loading/unloading of one pallet while machining on the other, drastically reducing downtime and increasing productivity.
- Better for Multi-Sided Machining: The design of HMCs is conducive to easy setup for multi-sided machining, making them ideal for complex parts requiring operations on several surfaces.
Limitations
- Cost: HMCs tend to be more expensive than VMCs, both in terms of initial investment and floor space requirements.
- Complexity: The operational sophistication and additional features like the pallet changer system demand a higher level of skill from operators.
Vertical Machining Centers (VMCs)
VMCs feature a spindle oriented vertically, perpendicular to the machine's bed. The workpiece is attached to a table that moves vertically (Z-axis) and horizontally (X and Y-axis), allowing the cutting tool to remove material from the top of the workpiece.
Advantages of VMCs
- Cost-Effectiveness: Generally, VMCs are less expensive than HMCs, making them accessible for smaller shops or businesses with limited budgets.
- Simplicity and Ease of Use: The straightforward design and operation of VMCs make them suitable for a wide range of machining tasks with minimal training.
- Flexibility in Part Setup: The vertical orientation allows for easier setup for a variety of parts, making VMCs versatile for different types of jobs.
- Visibility: Operators have better visibility of the machining process in VMCs, which can aid in monitoring and adjustments.
Limitations
- Chip Evacuation: Unlike HMCs, chip removal can be more challenging in VMCs due to the vertical orientation, potentially leading to tool wear and part contamination.
- Rigidity and Cutting Force: Although VMCs are suitable for a wide range of machining tasks, they might not match the rigidity and material removal rate of HMCs for particularly tough jobs.
Choosing Between HMC and VMC
The decision to opt for an HMC or VMC depends on various factors such as:
- Production Volume: High-volume production runs benefit from the efficiency and reduced setup time of HMCs, while VMCs might be more suitable for low to medium volumes.
- Complexity of Parts: Complex parts requiring multi-sided machining favor the design and capabilities of HMCs, whereas simpler parts can be efficiently machined on VMCs.
- Budgetary Constraints: The lower initial cost and operational expense of VMCs make them attractive for companies with tighter budgets.
- Available Space: Given their larger footprint, HMCs require more floor space than VMCs, a critical consideration for facilities with limited space.
Conclusion
Both horizontal and vertical machining centers offer distinctive advantages and are suitable for different manufacturing applications. HMCs stand out in high-volume production environments and when working with complex, multi-sided parts, offering superior efficiency, rigidity, and reduced downtime through pallet changers. VMCs, on the other hand, provide a cost-effective and versatile solution for a wide range of machining tasks, particularly for shops focusing on lower volumes or simpler parts. Understanding the unique attributes and applicability of these machines is crucial in making an informed decision that aligns with specific manufacturing objectives, ensuring optimal productivity, quality, and profitability in the machining process.