Machining centers are complex machines that integrate various components to perform a wide range of machining operations. Understanding the major components of machining centers is crucial for manufacturers seeking to optimize their processes and maximize the capabilities of these versatile machines. In this article, we will explore the five major components of machining centers, including the basic structure, spindle components, automatic tool changing system, CNC system, and auxiliary equipment.
Introduction to Machining Centers
At the heart of machining centers lies CNC (Computer Numerical Control) technology which orchestrates the automated execution of a plethora of machining operations such as milling, drilling, and turning. The synergy of the machine's components, governed by the precision of CNC, facilitates the creation of complex parts with unparalleled accuracy. Delving into the major components reveals the intricate engineering that underpins these indispensable manufacturing assets.
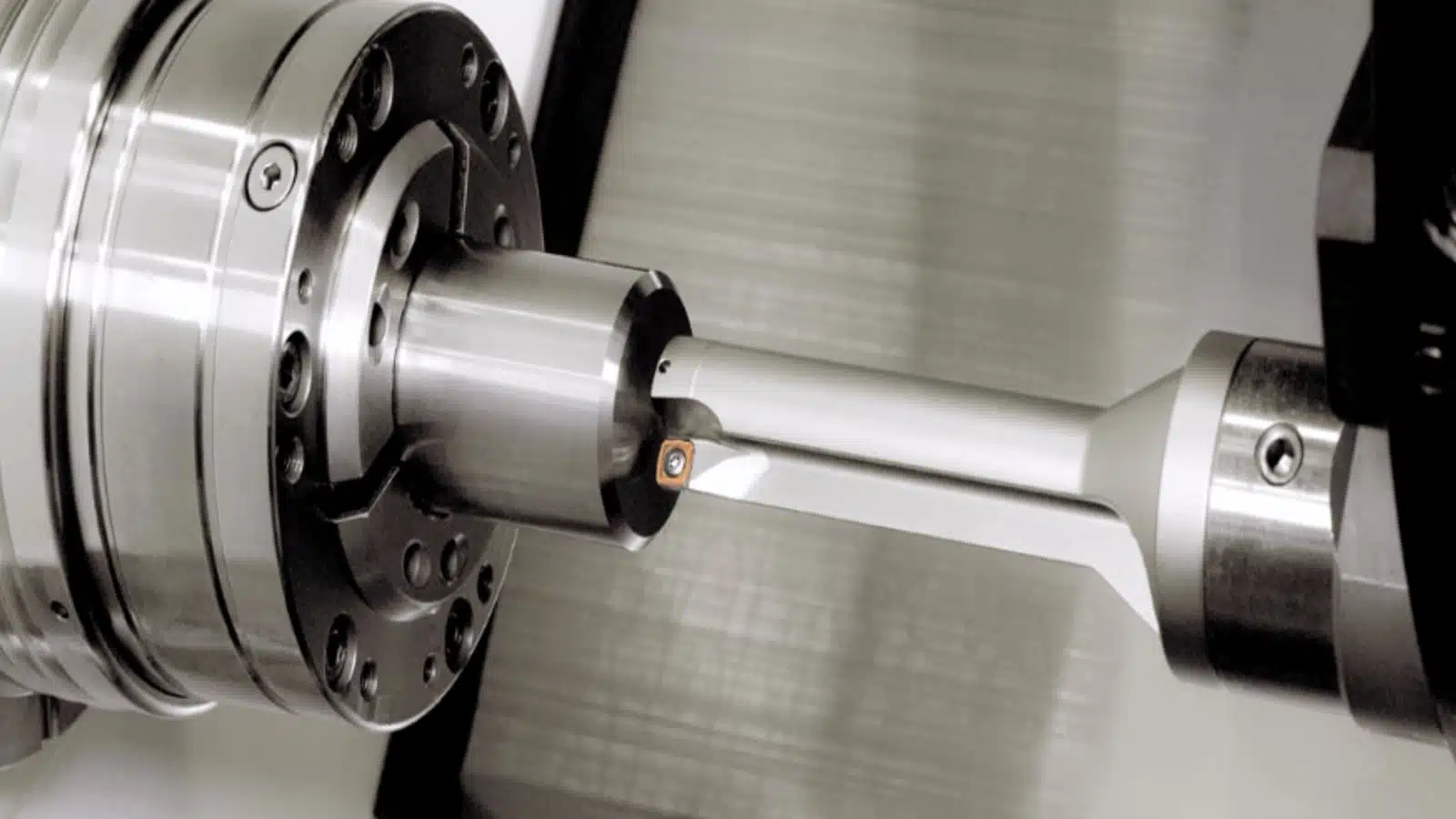
Basic Structure (Base Structure)
The foundation of a machining center is its basic or base structure, which encompasses the machine bed, columns, and the housing. This fundamental framework not only supports the operational components but also ensures rigidity and stability during machining processes.
Role and Importance
- Stability and Rigidity: The base structure is engineered to absorb and mitigate vibrations resulting from cutting operations, thereby ensuring optimal precision and surface finish.
- Support and Alignment: It provides the necessary support for other critical components, facilitating proper alignment that is crucial for accuracy in machining.
Spindle Components
The spindle components are at the core of a machining center's operation. This assembly includes the spindle box, spindle motor, spindle, and spindle bearings. The spindle itself holds and rotates the cutting tool, performing the actual cutting work on the material.
Role and Importance
- Cutting Tool Rotation: The spindle rotates the cutting tool at varying speeds, dictated by the machining requirements, thus directly influencing the quality and efficiency of the cutting process.
- Precision and Speed: Advanced spindle motors and bearings allow for high-speed operations while maintaining precision, significantly impacting productivity and part quality.
Automatic Tool Changing System
To enhance efficiency and reduce manual labor, machining centers are equipped with an Automatic Tool Changing (ATC) system. This system typically consists of a tool magazine that stores various cutting tools and a robot arm (or other mechanical means) to change the tools in the spindle automatically.
Role and Importance
- Efficiency and Productivity: By automating tool changes, the ATC system significantly reduces downtime between operations, enhancing overall productivity.
- Flexibility: The ability to automatically switch between a wide array of tools enables machining centers to execute complex machining tasks without manual intervention, adding to the machine's versatility.
CNC System
The CNC system is the brain of the machining center, directing the synchronized operations of the machine's components. It includes the CNC device, programmable controller, servo drive device, and an operation panel. These elements work in unison to interpret the programmed machining instructions and execute them with precision.
Role and Importance
- Control and Coordination: The CNC system precisely controls the movements of the machine's components, ensuring the execution of complex machining tasks with high accuracy.
- Programming Flexibility: Through the programmable controller and operation panel, operators can input and modify machining instructions, allowing for the customization of operations according to specific production needs.
Auxiliary Equipment
Machining centers are also complemented by an assortment of auxiliary equipment, which plays key supporting roles in the machining process. This category includes systems for eddy current sliding, cooling, chip removal, protection, as well as hydraulic, pneumatic, and detection systems.
Role and Importance
- Cooling and Lubrication: The cooling system controls the temperature of the cutting area, preserving tool life and ensuring the quality of the workpiece.
- Chip Removal: Efficient chip removal is vital to maintain the cleanliness of the work area and prevent damage to the workpiece or machine.
- Safety and Efficiency: Protection systems, along with hydraulic and pneumatic components, ensure the safety of operations and enhance the efficiency and longevity of the machining center.
Conclusion
The five major components of machining centers - the basic structure, spindle components, automatic tool changing system, CNC system, and auxiliary equipment - each play an indispensable role in the machine's function and efficacy.