In the high-stakes environment of modern manufacturing, the health and efficiency of CNC (Computer Numerical Control) machines play a pivotal role in productivity and operational success. CNC machine condition monitoring is a crucial aspect of predictive maintenance strategies, allowing manufacturers to anticipate potential failures and address them proactively. This article delves into the importance, methods, and benefits of CNC machine condition monitoring, highlighting how it integrates into manufacturing processes to enhance overall performance.
The Importance of Machine Condition Monitoring
CNC machines are integral to manufacturing processes, known for their precision and repeatability. However, like any mechanical system, they are susceptible to wear and tear, component fatigue, and unexpected failures, all of which can lead to costly downtime and reduced productivity. Implementing a robust condition monitoring system helps in detecting signs of potential issues before they escalate into major problems, thus maintaining continuous operation and optimizing machine performance.
Methods of CNC Machine Condition Monitoring
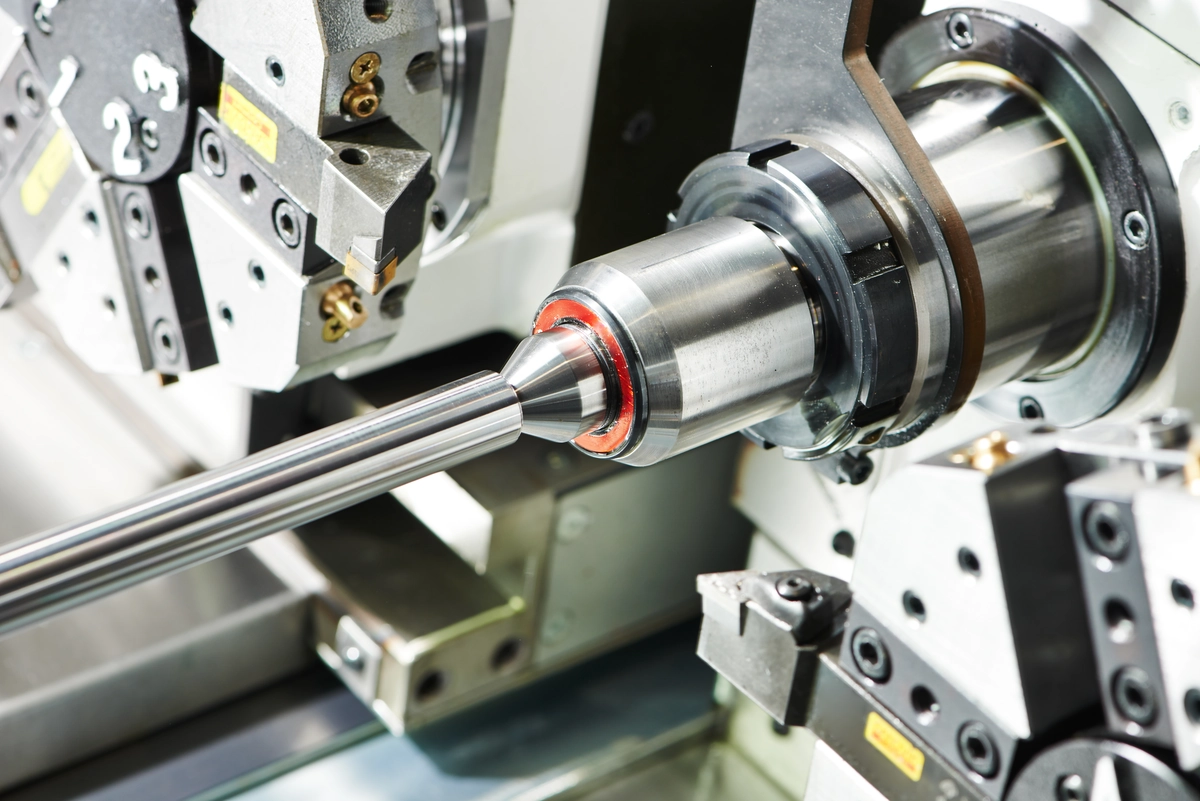
Condition monitoring of CNC machines involves various techniques and tools designed to assess the operational status of machinery. Here are some of the most effective methods:
-
Vibration Analysis
Vibration analysis is one of the most common methods used in machine condition monitoring. By measuring the amount and frequency of vibrations within the CNC machine, technicians can identify abnormal vibrations indicative of issues such as imbalance, misalignment, or bearing failures.
-
Thermal Imaging
Thermal cameras can detect overheating issues in CNC machines, which are often a sign of excessive friction, electrical failures, or lubrication problems. Monitoring temperature changes through thermal imaging helps in preventing overheating-related damages.
-
Acoustic Monitoring
This involves listening for changes in the noise or acoustic emissions from CNC machines. Unusual sounds can be early indicators of issues like bearing wear or gear faults.
-
Oil Analysis
Analyzing the debris and chemical composition of the machine's lubricant can provide insights into the internal condition of machine components. Contaminants or metal flakes in the oil can indicate wear or impending failure.
-
Performance Metrics Analysis
Monitoring key performance indicators such as cycle times, feed rates, and force measurements can help detect deviations from standard performance, which might signify developing problems.
Integration of Condition Monitoring Technologies
Advancements in IoT (Internet of Things) technologies have transformed CNC machine condition monitoring by enabling real-time data collection and analysis. Sensors attached to CNC machines can continuously record data on various parameters, which is then processed using advanced analytics to predict maintenance needs. This integration not only ensures timely maintenance but also enhances the precision of diagnostics.
Benefits of CNC Machine Condition Monitoring
Implementing condition monitoring in CNC machine operations brings several benefits:
- Reduced Downtime: By predicting failures before they occur, condition monitoring allows for planned maintenance rather than reactive maintenance after a failure, significantly reducing unplanned downtime.
- Increased Machine Lifespan: Regular monitoring and maintenance based on precise condition data can enhance the overall lifespan of CNC machines by ensuring that all components are operating within their intended specifications. Lunyee's
includes various types, and proper maintenance methods can help you use these equipment for a long time. - Optimized Maintenance Costs: Condition monitoring supports a predictive maintenance strategy, which is more cost-effective than preventive or corrective maintenance. By servicing machines only when needed, manufacturers can save on unnecessary maintenance costs and reduce wastage of parts and labor.
- Enhanced Safety: Regular monitoring helps in maintaining the machines in optimal condition, which reduces the risk of accidents caused by machine malfunctions, thus ensuring a safer working environment.
Conclusion
CNC machine condition monitoring is an essential practice in modern manufacturing that supports predictive maintenance strategies, enhances efficiency, and reduces operational risks. By employing sophisticated monitoring techniques and integrating advanced IoT technologies, manufacturers can ensure their CNC machines operate at peak performance, thereby maximizing productivity and extending the lifecycle of their equipment. As manufacturing processes continue to evolve and demand greater efficiency, the role of effective machine condition monitoring will become increasingly critical in achieving operational excellence.